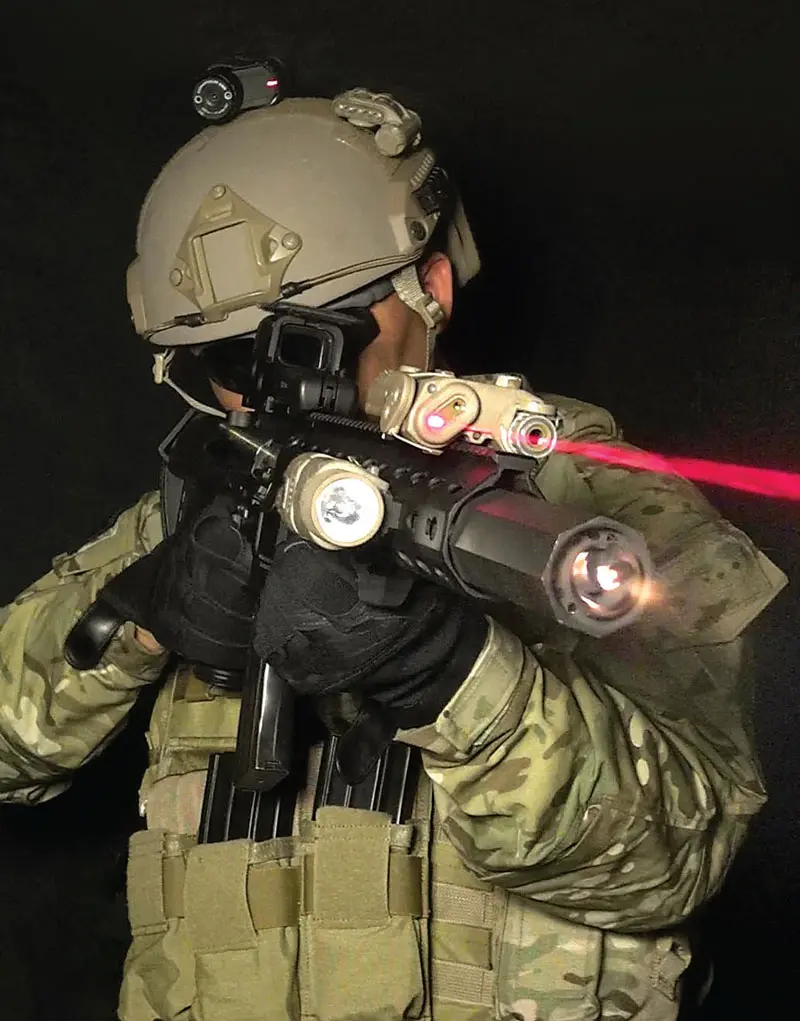
At SHOT Show this year, we discovered a new suppressor company owned and operated by former U.S. Army Special Forces guys. The claims made by Operators Suppressor Systems (OSS) with regard to their products made us, to say the least, skeptical. Their data sheet showed numbers relating to decibel reduction, point of impact shift, unit life expectancy, and back pressure reduction that were a little hard to believe. Needless to say, we wanted to see how these units would perform in person.
After contact was made, Russell Oliver, the owner of OSS and designer of the system, invited us to his facility in Murray, Utah to see for ourselves how the unit is made and, more importantly, how it functions. Russell began the visit with a quick tour of his 18,000-square-foot facility filled with state-ofthe- art machinery and the dedicated personnel making his products. He then spent several hours explaining his suppressor system, insuring we understood how it works and why.
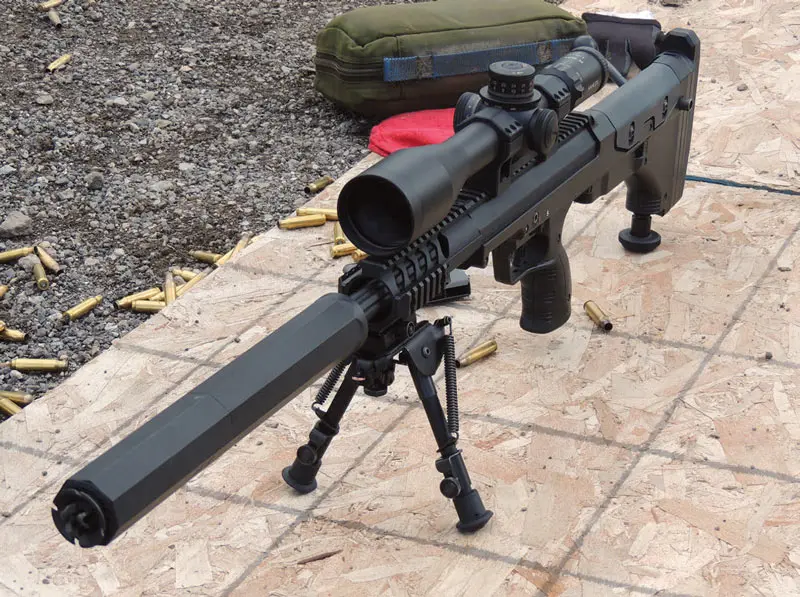
Table of Contents
UPGRADING THE SUPPRESSOR
Manufacturers have been making suppressors using essentially the same baffle design for over 100 years. While there have been improvements in materials, manufacturing and attachment techniques, the efficiency of these suppressors and the issues they create in the weapons they are attached to have not changed much until now. OSS has a product that not only improves on the traditional qualities expected of a suppressor, but also addresses most of the issues we have come to expect from this type of device.
Enter the OSS Modular Suppressor System. The system is made up of three basic components: the Flash Hider Muzzle Brake, Back Pressure Regulator, and Signature Reduction Module. Each component is modular and serviceable by the qualified user or unit armorer.
The Flash Hider Muzzle Brake (FHMB) is designed to replace the rifle’s existing flash hider or muzzle brake and allow for the rapid attachment of the Back Pressure Regulator. The unit initially seems long for its intended purpose, until you understand that the majority of it slides over the barrel, adding little to the overall length of the weapon. For example, if you had an A2-style flash suppressor and replaced it with the FHMB, you would add only ¾ inch to the length of the rifle. The unique design of the FHMB sets the stage for the rest of the unit to function as designed by redirecting gases as required.
The Back Pressure Regulator (BPR) is the heart of the OSS. This device controls expanding gases in a new and unique way, allowing for the “tuning” of the system to the intended weapon system, barrel length, and caliber. By adjusting the internal construction of the BPR, OSS is able to eliminate up to 95% of the back pressure seen in traditional suppressors, and increase bolt velocity by only 6%. The “over the barrel” design of the BPR adds only 3.9 inches to your weapon, and transfers the balance point of your weapon back toward the center point, making it easier to control. Amazingly, the BPR by itself reduces the audio signature of the rifle by 18dB and back pressure by 90%.
The final component is the Signature Reduction Module (SRM). This component is designed to reduce the audio signature of the weapon and can be had in various configurations to allow the user to decide the desired dB reduction. The units range in length from 2.3 to 5 inches, with the longer units providing additional sound reduction. Our test units were all equipped with SRM5s.
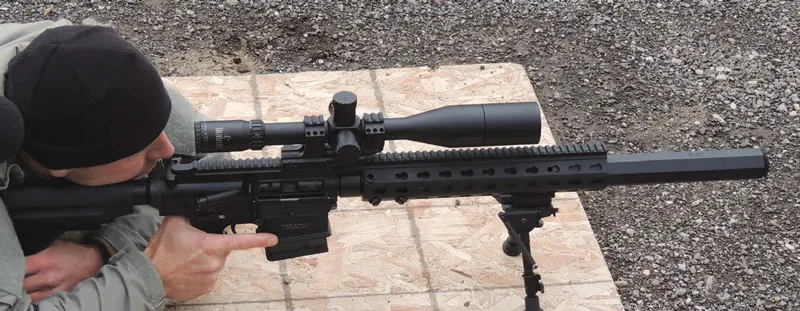
RANGE TESTING
Range firing with the OSS suppressor was both enlightening and exciting. Rolando Mata of OSS zeroed the rifles prior to testing, so we were able to begin our tests by firing with only the FHMB to get a baseline decibel reading and confirm zero. The BPR was then attached and a five-shot group fired to determine if there was any POI shift to the group.
This is typically a huge problem with traditional suppressors but has been overcome by OSS due in part to a unique self-aligning connection system. As each component is screwed together, they self-align for consistent placement. Each shot was recorded on a Larson Davis LXT Expert sound level meter to determine the peak decibel reading for the shot. The meter was held alongside the shooter’s head with the microphone next to the shooter’s right ear and pointed directly forward toward the muzzle to ensure an accurate reading.
After each string of fire, the target was inspected and the shots marked to assist in our POI shift measurements. Once we had the first group marked, we attached the SRM to the system and repeated the drill. Three different types of ammunition were used in each rifle to demonstrate that the system delivers consistent results from multiple ammunition types.
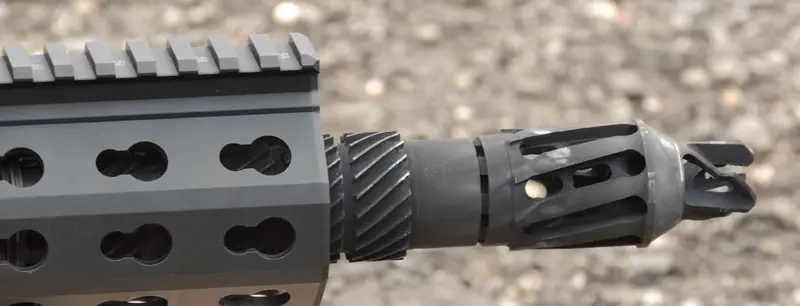
TEST RIFLES
Three different rifles were used in our tests: a Heckler & Koch MR762A1-SD and a Desert Tactical SRS-A1, both in 7.62x51mm, and an H&K MR556A1-SD in 5.56x45mm. Each rifle was equipped with an optical sight and fired prone using a Harris bipod. Results from all three rifles are shown in the accompanying tables.
Shooting the rifles equipped with the complete OSS system proved to be an entirely enjoyable experience, as ear protection was not necessary and recoil impulse was significantly reduced. The impression of firing the H&K MR556A1-SD was much like shooting a .22 long rifle caliber rifle—quiet, no recoil and very accurate.
As you can see in the tables, there was little to no change in zero with the OSS system attached. Normally we see a couple to several inches change in the POI after a suppressor is added. In fact, the varying temperature and changes in lighting on this stormy range day may have been responsible for the small changes we saw, as the majority of the groups being fired were consistently tight and on target.
BLOWBACK (OR LACK THEREOF)
Surprisingly, there was virtually zero blowback into the shooter’s face after each shot. Even on full-auto, the OSS system produced no noticeable blowback. OSS claims a 95% reduction in blowback with their system, and having fired them, I think OSS may be underestimating the reduction. During our range work, we fired several hundred rounds through multiple rifles and experienced zero malfunctions. On inspection, there was no more powder residue on the bolt and bolt carrier than expected from a non-suppressed system with the same number of rounds fired through it. This further validated the OSS claim of blowback reduction.
When asked about this lack of blowback, OSS advised that in conventional suppressors, the bolt is forced rearward by the operating system before the barrel has depressurized, causing high-pressure gas to be released from the barrel into the action, magazine and ejection port, exiting into the operator’s face. The OSS system creates an average of 30 to 50 PSI on the bolt face— a fraction of the 220 to 350+ PSI produced from any current baffle suppressor.
The suppressors remained tight throughout the firing sessions, even though they were mounted and dismounted numerous times. The components are designed to self-tighten during firing, and apparently do just that. But removal of the components after firing was accomplished by hand with no tools required.
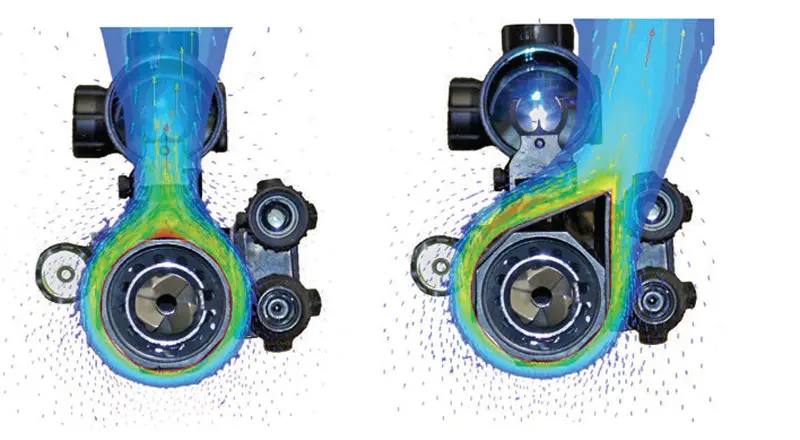
INCREASED BOLT SPEED
Another issue associated with traditional suppressors is increased bolt speed due to excessive pressure caused by the buildup of gas in the suppressor and barrel. OSS has engineered their system to maintain bolt velocity at less than 6% increase as compared to a bare muzzle.
Russell Oliver elaborated: “As the pressure is retained rather than released by the baffle-style suppressor attached to the muzzle, the operating system is under excess pressure for a longer duration of time than it was originally engineered. This increase forces the action open at an accelerated rate prior to the barrel depressurizing, causing extreme force on the op rod, bolt, carrier, upper and lower receivers, and causing final barrel depressurization via the chamber rather than the muzzle. The excess force exerted on the operating system causes accelerated wear on all the rifle’s components and can reduce the life of a weapon by 25% to 50%. As a substantially larger volume of high PSI gas is retained longer and released through the operating system and chamber, bolt velocity increases from 18% to over 40%, causing a multitude of extraction failures, failures to feed and double feeds.”
The shape of the OSS system provides several advantages. OSS increases the surface area of the unit by using an octagonal shape. With this they achieve 92% thermal efficiency as compared to 50 to 55% efficiency on a traditional suppressor. The OSS units also run at approximately half of the temperature of a traditional can and cool twice as fast.
Also of interest is that the mirage created by a hot suppressor is significantly reduced by the octagonal design (60% reduction claimed), as the heat waves tend to follow the hard angles off the top of the unit left and right of the bore line. In the near future, OSS will offer a patented accessory for those with round suppressors to assist with this problem.
The carrying balance of the weapon was not adversely affected as it normally is with traditional systems where the can is mounted completely forward of the muzzle. The overthe- barrel mounting seems to provide just enough of a shift toward the center of mass to make the rifle seem just slightly muzzle heavy.
INDOOR RANGE FIRING
After firing the rifles on the outdoor range, we returned to the OSS facility to shoot in their indoor range, affectionately known as the “closet” and in fact an 8’x12’ enclosed space made with drywall covered in carpet. The bullet trap is built into the forward wall. For those who have experienced firing rifles or SMGs in enclosed spaces, you know that this is a supreme test of the product.
Over-pressure in these tight quarters can really be uncomfortable and quickly lead to permanent hearing damage. We began with the Desert Tactical in 7.62x51mm. The first shot, even wearing quality hearing protection, really rang my chimes! The over-pressure was amazing. We then mounted the OSS system and fired again. The difference was almost unbelievable, and by the third round we felt safe to remove our hearing protection without suffering any discomfort during or after the shot.
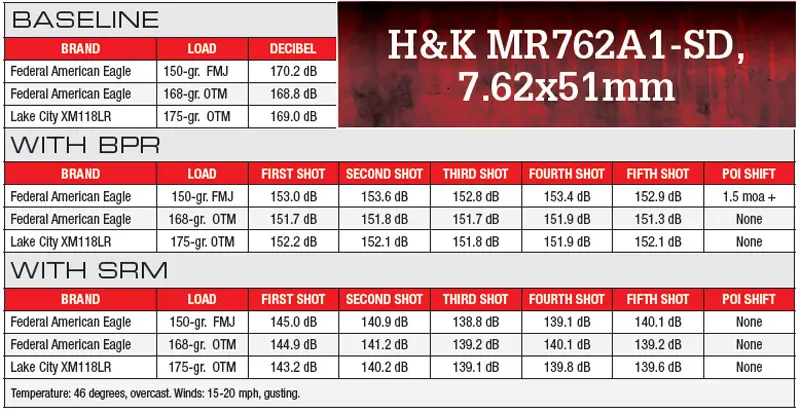
FULL-AUTO FIRE
We continued the indoor session by firing a Bravo Company Mfg 14.5-inch barreled carbine equipped with the OSS system. The carbine was fired in full-auto bursts and then complete 30-round magazines were fired, full-auto, to demonstrate several things. There were:
- No suppressor-induced malfunctions
- No significant over-pressure
- Almost no muzzle flash (3 lux is claimed by OSS and my own video revealed only small, barely noticeable sparks)
- No muzzle climb
- Almost no blowback
- Measured 461 degrees over the entire length of the BPR/SRM (a traditional suppressor runs at 1,000 degrees plus)
- Peak decibel reading of 141.6 dB (140 dB is considered “ear safe”) as compared to the semi-auto reading of 138 db
OSS not only builds a great product but they will guarantee that product for up to 10,500 rounds before any degradation of performance. They also guarantee that their suppressor will maintain factory specifications if their recommended sustainment guidelines are adhered to. In contrast, a traditional suppressor often starts to degrade after about 1,000 rounds if fired on full auto. The U.S. currently has military units deploying with up to four suppressors per weapon system in order to insure that they can make it through a single rotation and still have a functioning suppressor.
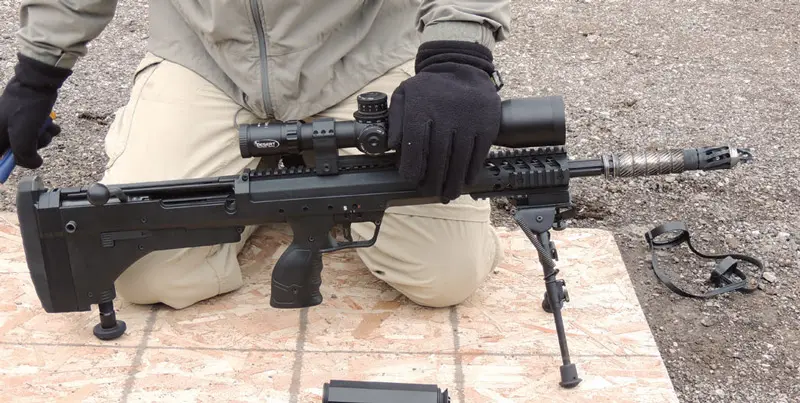
CONCLUSIONS
As our military evolved from black to smokeless powder to eliminate the visible signature from a fired round and protect our servicemen from the resulting return fire, we are now at the point in history where we need to evolve to eliminate the audio signature of our weapons systems for the same reasons.
Operators Suppressor Systems has the products we need to do just that. Unlike previous suppressor offerings, these can reduce the audio signature without adversely affecting the life of our weapons, causing radical shifts in POI, excessive heat and mirage, or blowback into the shooter’s face; and drastically reduce the over-pressure of the weapon when fired in close quarters.
The engineered improvements in weapon/suppressor reliability and increased life cycle make the OSS system extremely cost effective. Add in the predictable reduction in long-term hearing loss that is normally experienced by our military war fighters and you have a product that should be issued to all our troops.
We have tested many suppressors over our law enforcement and military careers. This is a game changer in all respects. All suppressors in the future will be judged by the OSS device as the yardstick.
Many groups and companies we have worked with in the past have made outlandish claims of superiority: “no first round pop,” “no perceptible flash signature,” “no impact shift between mounting and detachment of device from host weapon,” “no excessive heat signature,” “no excessive back-blast gas pressure through the ejection port,” and many others, all of which were debunked in very short testing periods.
This device truly performs to stated levels and amazed us completely. The guys at OSS are humble, down to earth, helpful and very professional. It was an honor and a pleasure to work with them on this project.